Understanding PP Plastic Hollow Boards: What You Need to Know
PP plastic hollow boards, also known as polypropylene hollow sheets, are widely recognized for their versatility and practicality. These boards are constructed from polypropylene, a type of plastic known for its excellent chemical resistance, durability, and lightweight properties. The hollow structure of these boards provides additional benefits such as insulation, impact resistance, and reduced material usage, making them an ideal choice for a range of applications.
PP plastic hollow boards come in various types, each designed for specific uses. For example, some boards are tailored for packaging, offering strength and flexibility to protect products during transit. Others are designed for construction or advertising, where durability and weather resistance are key considerations. By understanding the material properties and the different types of PP plastic hollow boards, you can better determine which board will best meet your needs.
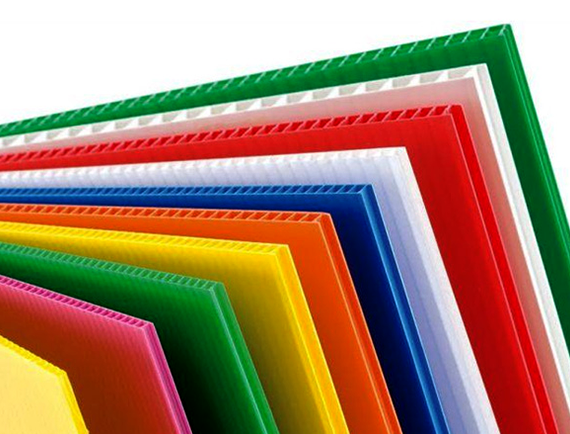
Key points to consider include the board’s thickness, which impacts its strength and flexibility, as well as its resistance to environmental factors like UV exposure and moisture. Whether you’re using these boards for indoor applications or outdoor projects, knowing the basics of PP plastic hollow boards will set you on the right path to making an informed decision.
Key Factors to Consider When Buying PP Plastic Hollow Boards
When purchasing PP plastic hollow boards, several critical factors should guide your decision-making process. These factors will ensure that you choose the right board for your specific needs, maximizing both the utility and lifespan of the product.
2.1 Thickness
The thickness of PP plastic hollow boards is a primary consideration, as it directly affects the board’s strength and flexibility. Thicker PP plastic hollow boards are generally more durable and can withstand greater impact, making them suitable for heavy-duty applications such as construction or industrial packaging. On the other hand, thinner PP plastic hollow boards may be more appropriate for lightweight applications, where flexibility and ease of handling are more important.
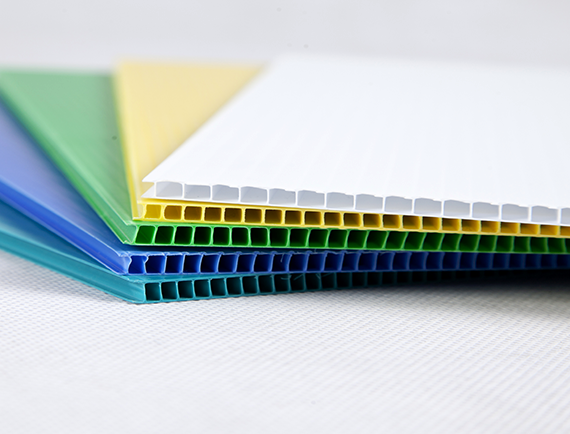
2.2 Durability
Durability is crucial, especially if the PP plastic hollow boards will be used in environments with harsh conditions, such as exposure to UV rays, chemicals, or moisture. High-quality boards are often treated to resist these elements, ensuring they maintain their integrity and appearance over time. When evaluating durability, also consider the PP plastic hollow board’s resistance to bending, cracking, and other forms of wear and tear.
2.3 Usage
The intended usage of the PP plastic hollow boards will significantly influence your choice. For example, PP plastic hollow boards used in outdoor signage need to be weather-resistant, while those used in packaging might prioritize lightweight and shock-absorbent properties. Identifying the specific needs of your project will help you select the right board type and specifications.
2.4 Cost-Effectiveness
While it’s tempting to opt for the cheapest option, considering the cost-effectiveness of the PP plastic hollow boards is vital. This means looking at the balance between price and quality. A more expensive board might offer better durability and performance, reducing the need for frequent replacements and ultimately saving you money in the long run. Compare prices across different suppliers and assess whether the additional features or enhanced quality justify the higher cost.
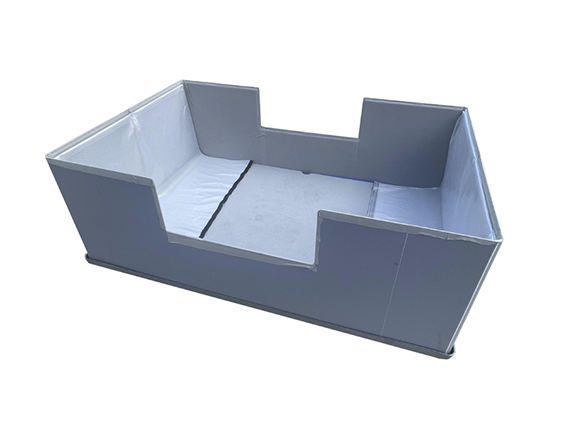
Comparing PP Plastic Hollow Boards: How to Make the Right Choic
3.1 Quality and Material Composition
Start by comparing the quality and material composition of the boards. Higher-quality PP plastic hollow boards are often made with purer polypropylene, offering better durability, resistance to environmental factors, and a longer lifespan. Boards with mixed or recycled materials might be less expensive but may not perform as well in demanding conditions. It’s essential to weigh the benefits of higher quality against the potential cost savings of lower-grade materials.
3.2 Cost-Effectiveness
Consider the overall cost-effectiveness of the PP plastic hollow boards by looking at both the initial purchase price and the long-term value. While some boards may have a lower upfront cost, they might require more frequent replacements or maintenance, leading to higher overall expenses. On the other hand, investing in a more durable and high-quality PP plastic hollow board could result in lower costs over time due to its extended lifespan and reduced need for repairs.
3.3 Supplier Reputation and Support
Another crucial aspect of comparison is the reputation of the suppliers and the level of support they offer. Reliable suppliers are more likely to provide consistent product quality, timely deliveries, and responsive customer service. Additionally, consider whether the supplier offers warranties or guarantees, which can provide added peace of mind. A trusted supplier may also offer technical support or advice to help you select the best PP plastic hollow board for your application.
3.4 Specific Application Requirements
Finally, compare how well the boards meet the specific requirements of your application. For example, if you need PP plastic hollow boards for outdoor use, prioritize those with UV resistance and weatherproofing features. If your application involves packaging, focus on boards that offer flexibility, shock absorption, and lightweight properties. Understanding the unique demands of your project will help you narrow down the options and choose the PP plastic hollow board that provides the best fit.
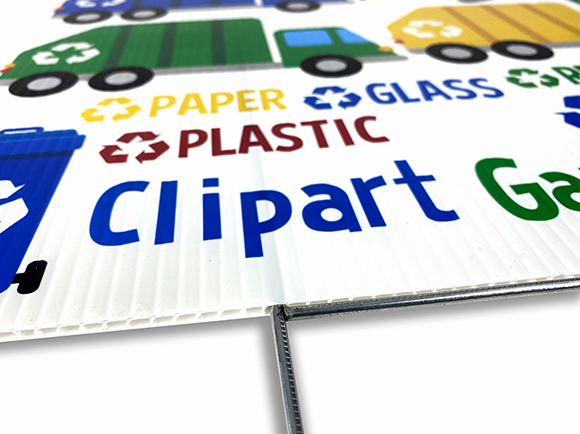
FAQS
What are the common thickness options for PP plastic hollow boards, and how do I choose the right one?
PP plastic hollow boards typically range in thickness from 2mm to 10mm. The right thickness depends on your application—thinner boards (2mm-4mm) are ideal for lightweight packaging and signage, while thicker boards (6mm-10mm) offer more durability and are better suited for construction or heavy-duty packaging.
Are PP plastic hollow boards suitable for outdoor use?
Yes, PP plastic hollow boards can be used outdoors, but it’s important to choose boards with UV resistance and weatherproofing treatments. These features protect the boards from sunlight, moisture, and temperature fluctuations, ensuring longevity even in harsh outdoor conditions.
How do I know if a PP plastic hollow board is of good quality?
Good quality PP plastic hollow boards are typically made from pure polypropylene, which provides better strength, durability, and resistance to chemicals and environmental factors. Check for certifications, material composition details, and reviews from other buyers to assess the quality of the board.
Can PP plastic hollow boards be customized for specific needs?
Yes, many suppliers offer customization options, such as specific sizes, colors, and surface treatments, to meet your unique requirements. Customization can also include adding features like anti-static properties or fire retardancy, depending on your application.
What are the main uses of PP plastic hollow boards?
PP plastic hollow boards are incredibly versatile and are used in a variety of industries. Common applications include packaging (especially for reusable and protective packaging), construction (such as wall panels and flooring), and advertising (like signage and display boards). Their lightweight yet durable nature makes them suitable for many different uses.
Conclusion:
Selecting the perfect PP plastic hollow board doesn’t have to be complicated. By considering key factors like thickness, durability, and cost-effectiveness, and by understanding the different types available, you can ensure that you’re making a smart investment. We hope this guide has provided you with the insights you need to choose the right board for your needs.